
Updates
Mastering Cost Management in Manufacturing
May 7, 2024
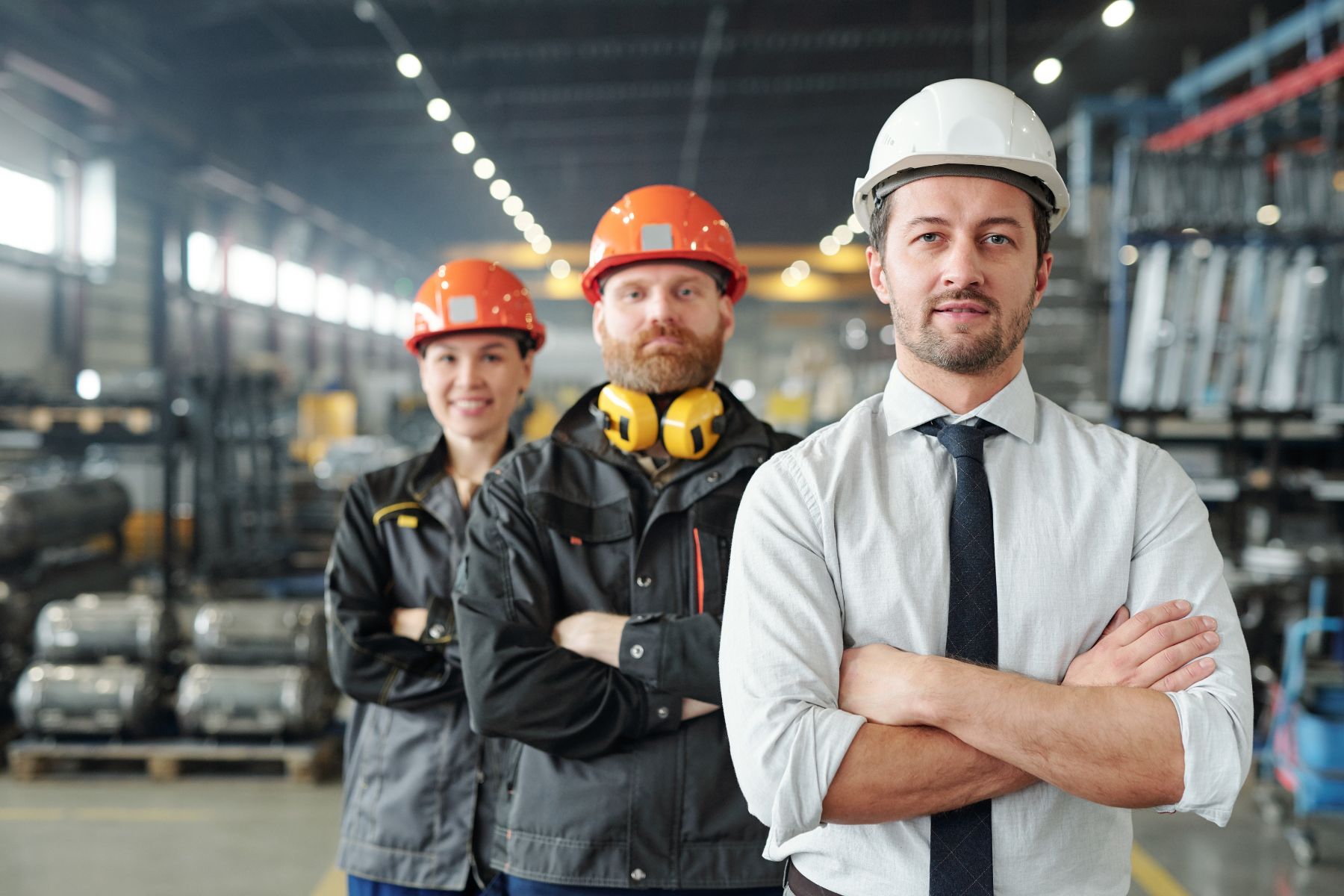
From Cost Control to Profit Maximization, Achieve Manufacturing Success with These Cost Management Strategies
In the competitive landscape of the manufacturing sector, controlling costs and optimizing resources are essential for achieving profitability and sustaining long-term success.
As Certified Public Accountants (CPAs) and business consultants, we understand the importance of implementing effective cost-management strategies to help manufacturing businesses thrive.
In this article, we'll discuss techniques for controlling costs, optimizing resources, and improving profitability in the manufacturing sector.
Lean Manufacturing Principles
Implementing lean manufacturing principles is a cornerstone of effective cost management in the manufacturing industry. Manufacturers can streamline operations, reduce costs, and enhance efficiency by identifying and eliminating waste throughout the production process.
Techniques such as 5S (Sort, Set in order, Shine, Standardize, Sustain), Kanban, and value stream mapping enable manufacturers to identify and eliminate non-value-added activities, leading to significant cost savings.
Just-in-Time (JIT) Inventory Management
Adopting a just-in-time inventory management approach allows manufacturers to minimize inventory holding costs while ensuring timely production and delivery of goods.
By synchronizing production with customer demand, manufacturers can reduce inventory carrying costs, optimize warehouse space, and minimize the risk of excess or obsolete inventory. JIT principles also promote efficiency in production processes, as resources are allocated based on real-time demand signals.
Strategic Sourcing and Supplier Management
Strategic sourcing involves identifying and partnering with reliable suppliers who offer competitive pricing, high-quality materials, and timely delivery. Manufacturers can reduce procurement costs, minimize supply chain disruptions, and ensure product quality consistency by negotiating favorable terms and establishing long-term relationships with key suppliers.
Effective supplier management practices, such as vendor performance evaluations and development programs, further reduce costs and improve operational efficiency.
Investment in Technology and Automation
Investing in technology and automation solutions can yield significant cost savings and productivity improvements in manufacturing operations. Automation technologies like robotics, CNC machining, and advanced manufacturing systems enable manufacturers to streamline production processes, reduce labor costs, and enhance product quality and consistency.
Additionally, implementing data analytics and enterprise resource planning (ERP) systems allows manufacturers to gain insights into cost drivers, identify areas for improvement, and make data-driven decisions to optimize resource allocation and maximize profitability.
Continuous Improvement and Cost Reduction Initiatives
Fostering a culture of continuous improvement and cost reduction is essential for driving sustainable cost savings in manufacturing organizations. Manufacturers can achieve incremental gains in productivity and efficiency over time by empowering employees to identify inefficiencies, suggest process improvements, and implement cost-saving initiatives.
Techniques such as Kaizen events, value engineering, and cost reduction workshops enable organizations to systematically identify and address cost drivers across all business aspects.
Charting a Path to Success
Effective cost management is critical for manufacturing businesses seeking to enhance profitability and maintain a competitive edge in the market. By implementing lean manufacturing principles, adopting just-in-time inventory management practices, strategically sourcing materials, investing in technology and automation, and fostering a culture of continuous improvement, manufacturers can control costs, optimize resources, and achieve sustainable growth and success.
As CPAs and business consultants, we are committed to helping manufacturing clients implement cost-effective strategies to maximize profitability and achieve their business goals. By leveraging our expertise and industry insights, we can assist manufacturing businesses in identifying opportunities for cost reduction, improving operational efficiency, and driving long-term financial success.
About Bowers
Bowers aims to offer helpful information to our clients and friends. Learn more about how we can help should your business need manufacturing services.
Bowers CPAs & Advisors has served private and closely held businesses with strategic financial advice for over 40 years. Whether traditional Tax and Audit, Client Accounting & Advisory Services, Business Valuation, Accounting/Bookkeeping, Forensic Accounting, or Financial Planning services, our approach is the same:
"Master an in-depth knowledge of our clients and their industry to provide proactive, innovative analysis and recommendations to build and maintain net worth."
At Bowers CPAs & Advisors, we set the tone by being readily available to our clients and maintaining close relationships built on integrity and trust. With 31 Partners and a staff of more than 130 professionals, Bowers CPAs & Advisors has offices in Syracuse, Rochester and Watertown, New York.
Disclaimer: To ensure compliance with requirements imposed by the Department of Treasury, we inform you any U.S. federal tax advice contained in this document or video is not intended for the purpose of (i) avoiding penalties under the Internal Revenue Code, or (ii) promoting, marketing, or recommending to another party any transaction or matter that is contained in this document.